激光加工设备正向下游各应用领域加速渗透,高功率技术突破国产品牌崛起将倒逼国内市场变革。
全球激光器市场超百亿美元,光纤激光器占比最大且增速高
激光产业链简述
激光已成为现代高端制造的基础性技术之一,具有举足轻重的地位。与激光相关的产品和服务已经遍布全球,形成庞大的激光产业。
激光设备的不断升级换代和新应用场景的拓展,驱动整个激光行业持续快速增长。
在传统HTH登陆入口网页 领域,低性能激光设备更新换代步伐加快,同时由于激光光束的突出性能,新的应用场景被不断开发,市场规模持续扩大。
工业激光是激光产业发展的核心。激光器是激光加工设备的核心部件,约占激光设备成本的30-60%。

激光产业链可分为三部分,上游主要包括光学材料及元器件、电控和机械件等,中游主要为各种激光器及其配套设备,国外主要厂商有美国的IPG公司、英国SPI,国内主要厂商有锐科激光、创新激光;下游则以HTH登陆入口网页 产品、消费产品、仪器设备为主。
国外厂商有德国通快、日本AMADA,国内厂商有大族激光、华工科技、亚威股份、德龙激光等。

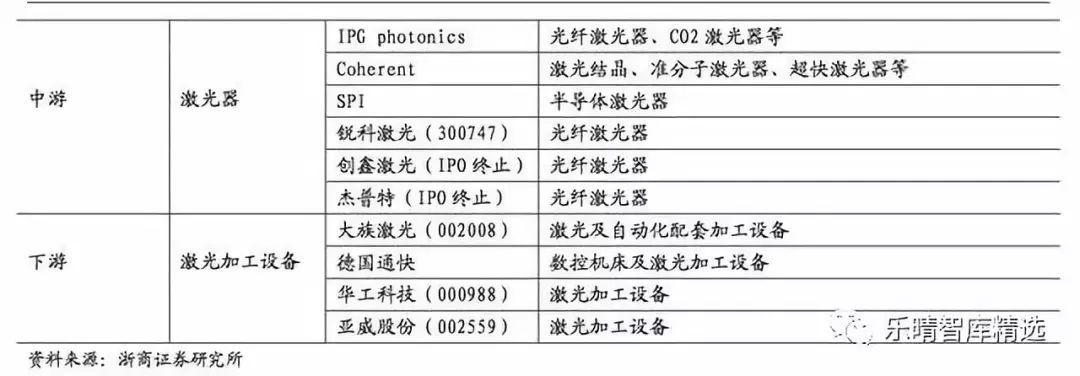
激光设备广泛应用于各领域。激光设备主要由光学系统、机械系统和数控系统组成,按照不同功率分类,一般讲平均功率在100W以下的激光器称为低功率激光器,100-1000W为中功率激光器,1000W以上的称为高功率激光器。
小功率激光器主要应用于电子、陶瓷、玻璃、五金、纺织、汽车零部件等轻工业制造,而高功率激光器一般运用于钣金加工、大型机械制造、石油化工、航空航天等重型设备的制造。
全球激光器市场持续增长,光纤激光器优势凸显
全球激光器市场超百亿美元,工业激光器增速最快。
全球激光器行业收入规模持续增长,根据StrategiesUnlimited的数据,2013-2017年,全球激光器市场规模从2013年的89.7亿美元增加至2017年的124.3亿美元,年复合增速为8.5%,其中2017年增速为18.16%。
其中,工业激光器市场规模从2013年的25亿美元增加至2017年的43亿美元,复合增速高达14.8%。
全球光纤激光器市场规模预计2025年达44亿美元。按照增益介质的不同,激光器主要可分为液体激光器、气体激光器、半导体激光器、光纤激光器和固体激光器等。
光纤激光器属于新一代固体激光器的一种,具有光电转换效率高、结构简单、光束质量好的特点,目前已成为材料加工的主流选择。
根据StrategiesUnlimited统计,全球光纤激光器在工业激光器中的市场份额保持逐年上升,从2013年的33.8%提升至2017年的43%,成为市场份额最大的工业激光器。
根据OptechConsulting的报告统计,2005-2017年,光纤激光器处于快速增长期,全球市场规模从1.05亿美元增长到22亿美元,年均复合增速达到29%,远高于同期激光器整体以及工业激光器的增速。
未来光纤激光器渗透率将继续增长,OptechConsulting预计到2025年全球市场规模将达到44亿美元,较2017年翻番。
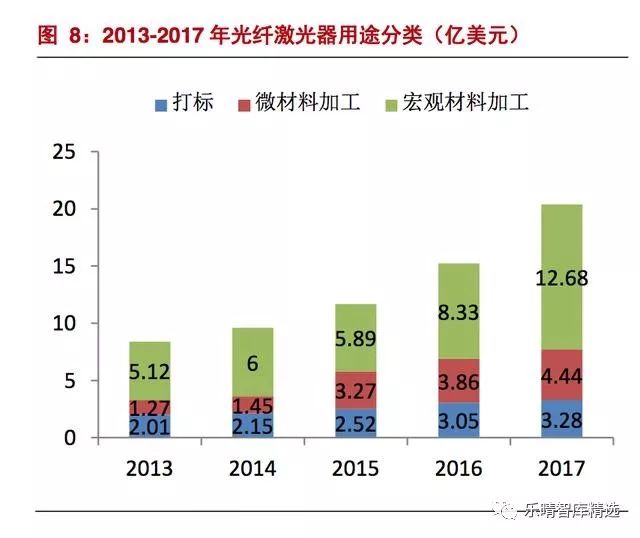
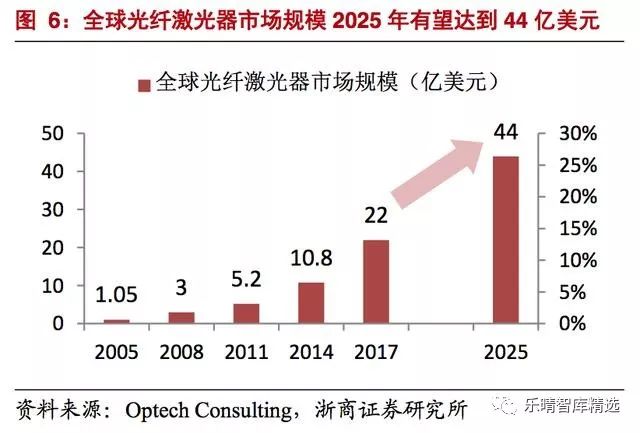
预计2021年亚太地区光纤激光器市场规模达13.26亿美元
亚太地区是全球工业激光器的最大市场。由于消费电子领域是工业激光器最大的终端应用产业,消费电子产品制造商的市场需求将使中国、日本、韩国、印度等国家和地区的工业激光器市场呈现大幅增长。
鉴于亚太地区工业部门的快速发展和光纤激光器低成本、高输出功率的优势,用于材料加工的光纤激光器市场空间巨大。
根据OFweek的数据,2018年亚太地区光纤激光器市场规模为8.72亿美元,2021年有望达到13.26亿美元,在此期间年复合增长率为14.99%。
光纤激光器正在逐步实现进口替代
千瓦级高功率光纤激光器突破促生繁荣市场
光纤激光器从零到百瓦功率发展了近四十年。早在1961年,美国科学家Snitzer提出在激光腔内使用稀土掺杂光纤可以得到稳定的单模激光输出,但受限于光纤制作和抽运光源,未能得到快速发展。
20世纪70到80年代是半导体激光器和光纤拉制工艺快速发展的二十年,由于抽运光很难高效耦合到直径几微米的纤芯,光纤激光器在很长时间只能产生mW级的激光输出。
1988年双包层光纤的出现使得光纤激光器输出功率实现了由mW级到W级的提升。
20世纪90年代随着大模场光纤技术的研制实现100W单模连续激光输出。
2004年,南安普敦大学的Jeong等世界上首次实现了千瓦级光纤激光输出。
千瓦级光纤激光器的出现使得高功率光纤激光真正走向了应用市场,各研究单位、创业公司如雨后春笋般出现,呈现出欣欣向荣的景象。
2012年,IPG曾报道了20kW的单模和100kW的多模光纤激光器,这也是目前光纤激光激光器的最大功率。
宏观材料加工是光纤激光器的主要应用方向
由于工业制造业的加速升级,光纤激光器向更高功率方向发展。
根据IndustrialLaserSolutions的研究报告,光纤激光器在工业领域用途可以分为打标、微材料加工、宏观材料加工三大类。
其中,微材料加工包括除了打标以外所有输出功率小于1000W的激光器应用;宏观材料加工包括所有输出大于等于1000W的激光器应用,主要为金属切割和焊接。
近年来打标的增速逐渐放缓,年复合增速为13.02%;宏观材料加工和微材料加工增速最快,年复合增速分别为25.45%和36.74%,2017年宏观材料加工规模为12.68亿美元,同比增长52.22%,占比62.16%。
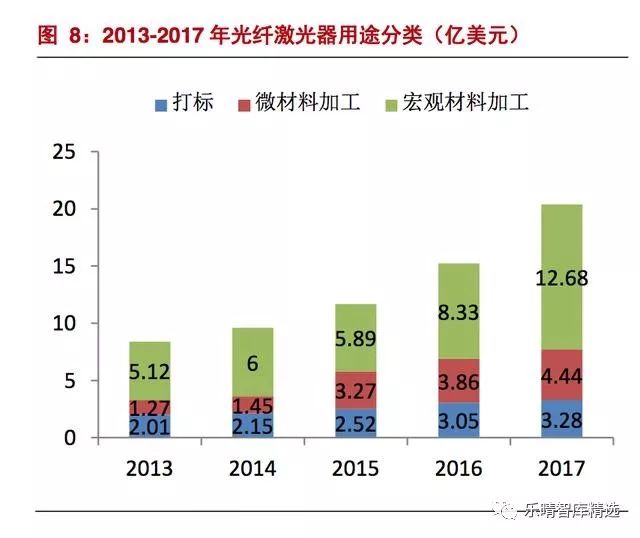
高功率激光器已打破外资垄断未来成长空间大
光纤激光器根据输出功率大小可分为三个层次:低功率光纤激光器(<100W)主要用于激光打标、钻孔、精密加工以及金属雕刻等;
中功率光纤激光器(≤1.5KW)主要用于金属材料的焊接和切割、金属表面的翻新处理;高功率光纤激光器(>1.5KW)主要用于厚金属板的切割、特殊板材的三维加工等。
目前低功率的已基本实现进口替代,中功率市场国产化率超过50%,而大功率激光器仍被外资厂商垄断,进口替代空间较大。
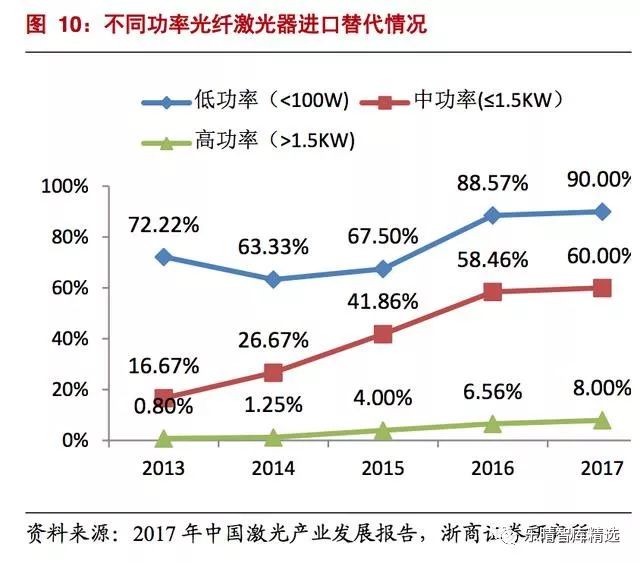
高功率激光设备是主流方向,中国市场增速远高于全球
全球激光器市场规模124亿美元,中材料加工为最大下游规模达到32亿美元
激光行业下游应用广泛,工业/材料加工激光器市场占比最大,达到34%。2017年全球124.3亿美元激光器市场中,材料加工是最大的应用市场,占比约34%,市场空间约43亿美元。其次是光通信和光刻市场,分别占比33%、8%。
激光焊接在材料加工市场提升空间很大。在材料加工方面,工业激光器主要用于切割、打标、金属精加工、金属焊接等,其中切割和打标为最重要的两个应用领域。
2017年,全球工业激光器在材料加工方面的应用中,切割应用占35%,焊接应用占16%,打标应用占15%。
激光切割占比高,主要原因在于激光切割机是通用型设备,推广比较快,焊接的工艺定制化较多,且下游客户十分分散,工艺定制化需要大量的集成设备商去做开发,推广相对复杂。
随着激光渗透率的不断提升,激光焊接增长空间很大。

激光加工设备全球市场135亿美元,中国市场288亿元,增速12%远高于全球增速
中国激光加工设备市场达288亿元。
全球材料加工激光设备市场近几年增速平稳,根据OptechConsulting的数据,全球材料加工激光设备市场规模从2012年的102亿美元,增长到2017年的135亿美元,年均复合增速为5.8%。
中国已逐渐成长为激光加工设备的重要市场,根据中商产业研究院的统计数据,中国激光加工设备市场规模从2012年的164亿元增长至2017年的288亿元,年均复合增速达到11.9%,远高于全球增速。
高功率激光设备:激光切割逐步替代传统机床设备
高功率激光器广泛应用于汽车制造、航空航天、化工、军工等领域。传统高功率加工主要由传统冲床、电阻焊等切割焊接设备来实现,效率低、精度差、损耗高,已无法满足制造升级的需求。激光器对传统设备的加速替代已渐趋明显。
据中国报告网数据,2017年全球用于材料加工的高功率激光器市场规模约14.92亿美元,占激光器市场的14%,材料加工用激光器的48%。
目前国内仅冲床加焊接市场就有近千亿规模,而国内大功率激光设备市场规模仅在100亿元左右,激光加工渗透率仍处于较低水平。

高功率激光切割设备主要替代传统数控设备。激光切割机是由激光器发出的激光束经透镜聚集形成极小的光斑(功率密度高达10^6-10^9W/cm^2),焦点处工件被高温瞬间汽化,再配合辅助气体将汽化的金属吹走,从而切穿成一个小孔。
随着机床移动,无数个小孔衔接起来构成要切的外形。由于激光切开频率十分高,所以每个小孔衔接处十分光滑。激光切割具备高速高精密、可重复性、异形切割、产能大、材料适应性强等优势。
据观研天下数据,目前传统冲床市场规模在200-300亿元,激光设备仍有巨大替代空间。
下游新兴市场需求旺盛,长期看好激光设备行业
新能源汽车:动力电池与新能源车成长空间广,加工工艺及轻量化需求逐渐升级
新能源车朝着车身轻量化和动力电池集中度提升两个方向发展。
激光切割和焊接技术是实现轻量化车身的关键制造技术。
汽车轻量化技术主要通过三种途径来实现:
1)轻质材料的比重不断攀升,铝合金、镁合金、钛合金、高强度钢、塑料、粉末冶金、生态复合材料及陶瓷灯应用;
2)结构优化和零部件的模块化设计水平不断提高,如采用前轮驱动、高刚性结构和超轻悬架结构等来达到轻量化的目的;
3)在成形方法和联接技术上不断创新。激光切割和激光焊接就以独特的优势,成为了实现汽车轻量化的重要技术手段。
就激光焊接来说,激光焊接是无接触性的,在加工过程中,可以不触碰产品就能实现精密焊接,而传统的连接方式,有的是靠螺丝紧固,有的是靠胶粘连接,并不能满足现代汽车制造中对精密性和坚固性的要求,并且传统的方式也不适用于连接新材料。
相比之下,激光焊接在连接的坚固性、无缝性、精密性和清洁性上都实现了工艺的跨越式进步,将成为未来重要的成型方式。
激光焊接是电池制造的重要工艺。激光焊接是唯一一种非接触式、高精度、高效的焊接方式;
可以经济快速的进行电池结构件焊接及密封,激光加工通常包括激光切割、激光焊接、激光表面处理等。在整个动力电池制造,包括电芯、模组和pack中有约19个主要构件部位需要焊接,其中:11个焊接目前必须用激光焊接;5个焊接可能用到激光焊接,只有三个焊接不会使用激光焊接。
方壳电池中,密封钉、盖板组件以及封口都需要用到激光焊接;而在圆柱电池及模组中,需要用到激光焊接的部分有极耳、盖帽、汇流排等。
激光焊接已经成为汽车制造中标准工艺。
汽车中应用到的激光设备主要用在主线焊接和离线零部件加工上:主线焊接即对汽车整个车身进行装配过程。
另外在汽车制造的过程中,除了主线焊装工艺中对白车身、车门、车架等零部件的加工,还有大量不在主线上制造的零部件可以用激光加工,例如发动机核心部件的淬火、变速器齿轮、气门挺杆、车门铰链焊接等等。
目前我国汽车制造设备市场空间预计1500亿元以上,其中汽车焊装自动化设备约占整体设备投资的25%左右,市场空间约400亿人民币。
消费电子:苹果引领全球消费电子工艺创新,5G有望带动新一轮设备创新
随着激光加工技术的发展,激光加工在手机制造中有多处应用,例如激光打标可应用于手机LOGO雕刻、表面二维码标记、蓝宝石内雕隐性二维码等;
由于手机防水性要求越来越高,小孔径加工选择激光钻孔更为合适;蓝宝石玻璃手机屏幕激光切割、摄像头保护镜片激光切割、FPC柔性电路板激光切割等;手机背板、电池等用激光焊接。
半导体&OLED:新兴市场有望维持可观成长
iphone引领OLED潮流,柔性OLED供不应求
iPhone确定采用柔性OLED。苹果向三星预定8000万块柔性OLED屏幕,三星因此追加70亿美元扩建工厂。苹果为Iphone9向三星续订1.8亿块柔性OLEd屏幕。此外iwatch也采用柔性OLED。
三星产能仅够三星和苹果需求,全球产能紧缺。iphone采用柔性屏幕后,HOV将会积极跟进,但三星的产能仅满足三星自身和苹果的需求。除了三星,其他厂商良率达不到要求,全球柔性OLED产能紧缺。
国内OLED产线加速投资,2019-2021年投资总额达2224亿
随着面板产能向国内转移,国产替代进口将是大势所趋。国内厂商如京东方、维信诺、和辉光电、天马、信利、华星等皆有布局,积极投建OLED线,根据OFweek统计,国内目前已经投产的面板生产线为27条,在建和规划中的生产线还有17条。
当前OLED生产线已投产有7条,未投产的有7条,有望带动对相关激光设备需求的增加。
OLED产线投资带动激光设备2019-2021年总需求达153亿
激光加工在OLED面板生产中至关重要。OLED面板的制造主要分为背板段、前板段和模组段三道工序,激光工艺贯穿始终。在背板段主要是准分子激光退火,前板段主要是LLO激光剥离及柔性切割,模组段主要是切割、测试修复及窄边框加工等。
根据上述统计,“十三五”期间国内厂商计划投产的产线投资总额至少3000亿,OLED产线投资中80%左右是设备投资。
其中工艺LTPS和LLO中需要ELA准分子激光器,切割工艺中需要紫外和飞秒激光设备,激光加工设备占整个OLED生产线投资额比重较高,通常在7%左右。因此,根据测算2020年以前OLED产线投资对激光设备的总需求至少达到173亿元,平均每年约有50亿以上。
作者:闻茗萱、潘贻立转载请注明出处。