随着科学技术的发展和制造技术的进步,产品质量和品种多样化的要求日益提高,中、小批生产的比例明显增大,促使数控机床不断向着高效率、高质量、高柔性和低成本的方向发展。另外,数控机床作为柔性制造单元、柔性制造系统及计算机集成制造系统的基础设备,对其中的数控装置、伺服驱动系统、程序编制、检测监控及机床主机等组成部分提出了更高的要求。
1、数控系统的发展。数控系统的发展是数控技术和数控机床发展的关键。电子元器件和计算机技术的发展推动了数控系统的发展。最初的数控系统使用电子管器件,后来使用晶体管和印制电路板,20世纪60年代末期开始使用小规模集成电路器件,这些都是所谓的硬线数控系统。20世纪70年代以来,随着计算机技术的发展,出现了以小型计算机、微处理器为核心的计算机数控系统(CNC)。现在,它已被广泛采用并占据绝对的优势。
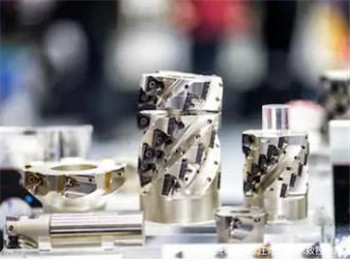
(1)数控系统的中央处理器。数控系统的中央处理器(CPU)已由8位字长增加至16位或32位,时钟频率由2MHz提高到16MHz、20MHz或32MHz,最近还出现了64位CPU,并且开始采用精简指令集运算芯片RSC作为CPU,使运算速度得到进一步提高。此外,大规模、超大规模集成电路和多个微处理器的应用,使数控系统的硬件结构标准化、模块化和通用化,使数控功能可根据需要进行组合和扩展。
(2)数控系统配备有多种遥控和智能接口。接口如RS-232C串行接口、Rs-422高速远距离串行接口及DNC接口等。配备DNC接口的数控系统,可以实现几台数控机床之间的数据通信,也可以直接对几台数控机床进行控制。此外,在数控系统中采用MAP等高级工业控制网络或 Ethernet(以太网),为解决不同类型、不同厂家生产的数控机床的联网和数控机床进入FMS和CMS等制造系统创造了条件。
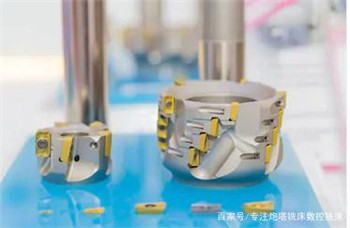
(3)数控系统具有很好的操作性能。数控系统上设置了很好的人机界面,普遍采用薄膜按键,减少了指示灯和按键数量;大量釆用菜单选择操作;彩色CRT显示屏,不仅可以显示字符、平面图形,还能显示三维动态立体图形,使操作越来越简便。
(4)数控系统的可靠性大大提高。数控系统大量采用了高集成度芯片、专用芯片及合成集成电路,减少了元器件数量。电子元器件采用表面安装工艺(SMT),出现了三维高密度安装。元器件经过严格筛选,提高了硬件质量,降低了功耗,极大地提高了系统的可靠性,使数控系统的平均无故障时间(MTBF)达到10000~36000h。
(5)开发式体系。20世纪80年代末、90年代初出现的CNC系统的结构硬件、软件和总线规范均是对外开放的,为数控设备制造厂家和用户二次开发具有各自技术特色的系统提供了有力的支持。
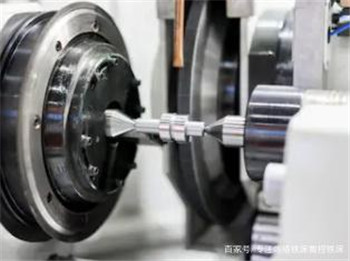
2、进给伺服系统的发展。进给伺服系统是数控机床的重要组成部分,它的电路、电动机及检测装置等的技术都有极大的提高。
(1)永磁同步交流伺服电动机逐渐取代了直流伺服电动机,提高了电动机的可靠性,降低了制造成本,基本上无须维修。
(2)伺服驱动电路中的位置、速度和电流控制环节部分实现了数字化,甚至以单片机或高速数字信号处理器为硬件基础进行全数字化控制,与CNC系统的计算机有双向通信联系。这样避免了零点漂移,提高了位置与速度控制的精度和稳定性;由于采用软件控制,故系统可以引用多种控制策略,容易改变系统的结构和参数,以适应不同机械负载的要求,有的甚至可以自动辨识负载惯量,并自动调整和优化系统的参数,从而获得最佳的静态和动态控制性能和效果。
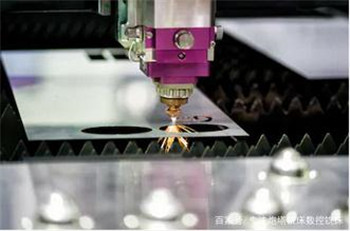
(3)采用高速和高分辨率的位置检测装置组成半闭环和闭环位置控制系统。增量式位置检测编码器达到10000脉冲/r,绝对式编码器可以达到100000脉冲/r和0.01m/脉冲的分辨率。分辨率为0.1μm/脉冲时,位移速度可达240m/min,这极大提高了位置控制的精度,即机床的定位精度。
(4)进给伺服系统不但可以实现丝杠螺距误差的补偿,而且使热变形误差补偿和间误差补偿取得了显著的成效。综合误差补偿技术的应用可以将加工误差减小60%左右。
3、数控机床编程技术的发展
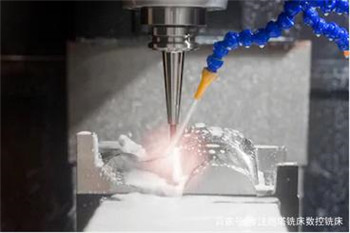
(1)数控机床的自动编程系统除语言编程系统外,图形编程也取得了长足的发展,增加了自动编程的手段。实物编程和语言编程也得到了发展。
(2)从脱机编程逐渐发展到在线编程。脱机编程是指由手工或编程计算机系统完成程序编制,然后再通过输入装置输入到数控系统内。现代的CNC系统具有很强的运算能力、很高的运算速度和很大的存储容量,可以将自动编程的很多功能植入到数控系统里,使零件的加工程序可以在数控系统的操作面板上在线编制,如 FANUC公司的 SymbolicFAP就是采用这样的编程方法,也可称之为图形人机对话编程。有的数控系统还具有空间曲面插补功能,插补软件可根据存放在数控系统内的空间曲面数学模型,插补加工出曲面轮廓,极大地简化了编程和程序输入,提高了加工的可靠性。
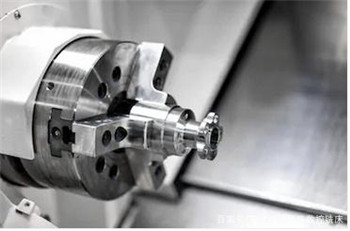
(3)在线编程过程中,数控系统不仅可以处理几何信息,还可以处理工艺信息,数控系统内设有与该机床加工工艺相关的小型工艺数据库或专家系统,系统可以自动选择最佳的工艺参数。
4、数控机床的工况检测、监控和故障诊断。现代数控机床上装有工件尺寸检测装置,对工件加工尺寸进行定期检测,发现超差则及时发出报警或补偿信号。红外、超声发射等监控装置可对刀具工况进行监控,遇有刀具磨损超标或刀具破损时,系统能及时报警,以便调换刀具,从而保证加工产品的质量。
目前,CNC系统中已经采用了开机诊断运行诊断通信诊断和专家诊断系统等故障自诊断技术,对故障进行自动查找分类、显示及报警,以便于及时发现和排除系统的故障。
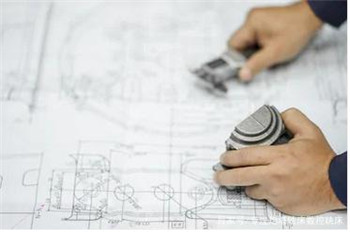
5、采用功能很强的可编程控制器。对于数控机床辅助功能的控制,以前都采用继电器逻辑硬件电路,而且要由用户设计制造。现代数控机床广泛采用内装型或独立型可编程控制器PC( Programmable Controller),它有专用的32位微处理器,基本指令执行时间是0.2 us/step,有梯形语言程序16000tf以上,可以采用C语言或Pas语言来编制PC程序,程序容量为68-256KB,在PC与CNC之间有高速窗口。采用C语言编程时,可以在个人计算机的开发环境下工作。利用PC的高速处理功能,使CNC与PC有机地结合起来,而且可以利用梯形图( Ladder)的监控功能,使机床的故障诊断和维修更加方便。
6、机床的主机。数控机床的主机也有很多新的发展。表现如下:
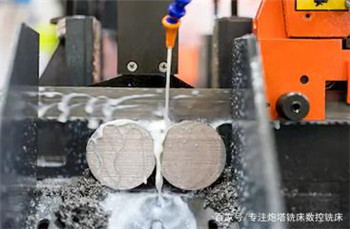
(1)主运动部件不断实现电气化的高速化。为了提高主运动的速度和调速范围,减少机械传动链,除采用直流调速电动机和交流变频调速电动机驱动主轴部件外,近年来更有采用内装式主轴电动机的机床出现,将主轴部件做在电机转子上,从而大大提高了主轴转速,主轴转速最高可达10000-1000ymin,而且仅用1.8s即可从零升到最高转速。
(2)增加加工功能。集中工序可以提高生产率和工件的形位精度。例如,采用自动换刀装置、自动更换工件机构、数控夹具等,开发出铣镗加工中心、车削加工中心等机床;采用转位主轴头架,形成五面加工能力。
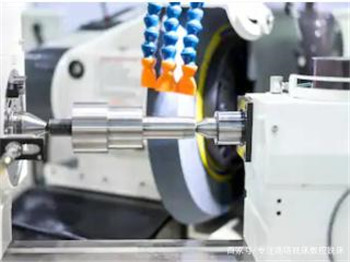
(3)采用机电一体化和全封闭式结构。数控机床将过去与主机分离的数控装置、强电控制装置和液压传动油箱等设备全部与主机合为一体,使结构紧凑,减少管线,减小占地面积;零件加工区域完全封闭在可以窥视的罩壳内,并采用自动排屑装置,改善了加工环境和条件;采用气动、液压机构以控制各种辅助运动机构,利用集中的压缩空气动力,以消除液压泵的耗能、发热和噪声等缺陷。
(4)主机的大件采用焊接结构和合理的结构形式,可在减轻机床自重的情况下,获得极高的结构刚度和抗震性。采用无级调速电动机,缩短机械传动链的长度,减小噪声,提高机械效率。采用低摩擦阻力的滚珠丝杠螺母副、静压丝杠螺母副、滚动导轨、静压导轨及贴塑导轨等传动、导向元件,极大地提高了传动刚度,减小了摩擦阻力,从而提高了进给运动的动态响应性能和低速运动的平稳性能。
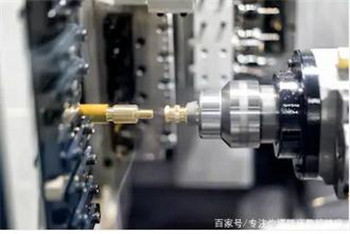
转载请注明出处。