但如果你开的是一辆保时捷959呢?对于这种极其稀有的车辆,想要自行购买它需要的零件绝非易事。
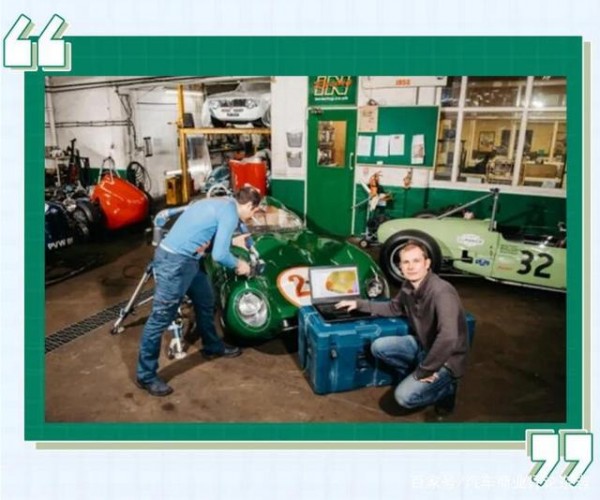
该技术选用激光作为能量源,按照三维CAD切片模型中规划好的路径在金属粉末床层进行逐层扫描,扫描过的金属粉末通过熔化、凝固从而达到冶金结合的效果,最终获得模型所设计的金属零件。
保时捷使用这种工艺——称为增材制造,因为它们涉及到添加材料层——为其老款车型生产了约30个零部件,要是用传统方式制造工具生产这些零部件的话,成本将高得令人望而却步。
保时捷之外呢?在整个汽车行业,大大小小的多家公司都在使用相同的技术生产各种产品,从模具的原型或样板部件到一次性的功能部件。它们被冠以逆向工程之名,因为涉及到对一个成品组件进行解构,以确定如何重新制造它。
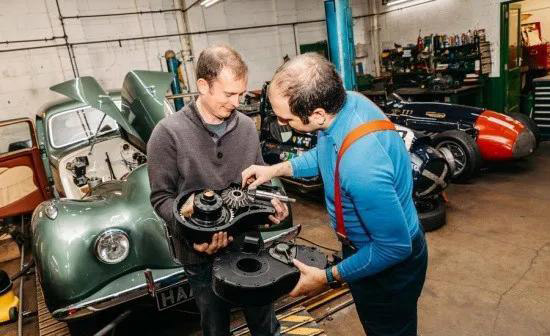
进入车间,看到的都是稀有的车型,比如1959年的Tec-Mec玛莎拉蒂;1959年的莲花15,曾由赛车手格拉汉姆·希尔(Graham Hill)驾驶;几辆Cooper Bristol赛车和1965年的阿尔法·罗密欧GTA。
但与INRacing车间里的坡道、车床,甚至是一个巨大的五轴数控铣床相比,阿利斯泰尔·皮尤(Alistair Pugh)创立的A2P2看起来更像是一个高科技公司,角落里的一个3D打印机正在安静地工作着。
房间另一边的3D激光扫描仪或许更引人注意。它的末端是一个探针,固定在一个坚固的金属桌子上,并与一台笔记本电脑相连。
皮尤的同事阿尔贝托演示了如何通过全面地将探针绕着部件移动,就可以捕获并数字化它的每一个维度,包括螺旋孔的内部表面。之后,得到的精确数字结果被转换成3D打印机的CAD文件或工程制图。
这么来看,好似动一动探针和鼠标就把问题解决了。对此,皮尤指出,如何从制造的角度解释数据和了解什么是可行的生产方案才是关键。
皮尤之所以这么说,一方面是他本来就毕业于工程学相关专业,另一方面,他的公司与INRacing、福特、阿斯顿·马丁和捷豹展开过合作,可以说是从实际经验出发。事实上,正是INRacing借给了皮尤12.5万英镑来购买他的第一台扫描仪。
这家公司最引以为傲的成就之一,是制作了一辆非常罕见的战前双门轿跑车的数字化版本,而且是仅靠该车的轿车版本和一些照片完成的。
“由于没有现有的模型可用,我们不得不扫描其轿车版本的底盘、驾驶舱,后轴和发动机,以确定轿跑版该有的支撑点和主要机械的位置。”皮尤指着车间里的一个部分组装起来的框架说,“尺寸是1:1的,看起来就像一件特别复杂的自组装家具。”
依靠现代技术可以让遗失已久的汽车起死回生,这是一件鼓舞人心的事。而现代经典的汽车也能通过这种新方式得到零部件供应上的改变。
我们来看看法国波尔多的GRYP公司是怎么做的。几年前,三位年轻的工程师创立了这家公司,专门从事3D打印技术,制造小众的或者根本不可能找到的旧款(主要是现代经典款)汽车零部件。
“我们做过的汽车零件从1929年到2000年的都有,但更多的是之后年代的,因为较新的车上用到了更多塑料材料。”GRYP联合创始人巴斯蒂安·梵仑斯(Bastien Vanlathem)表示,“对于老款汽车,虽然原始部件可作为参考,但我们可以用包括碳纤维在内的复合材料制造出比铝更耐磨的部件,还可以纠正原设计中的缺点。”
转载请注明出处。